Koska Reeves Helm
Koska Reeves begegnete uns in der abslolut fantastischen Serie „Der Mandalorianer“. Sie war ein Mitglied der „Night Owls“, des mandalorianischen Widerstands unter Führung von Bo-Katan Kryze wurden. Spektakulär war der Angriff auf den imperialen Gozanti-Klasse-Frachter mit Bo-Katan, Axe Woves und Din Djarin. Die Kostüme der Night Owls haben uns direkt begeistert und das Besondere daran war, dass es super geniale weibliche Heldinnen mit spektakulärer Amor war. Das erschien uns direkt bedeutend attraktiver, als eine weibliche Stormtrooper Armor
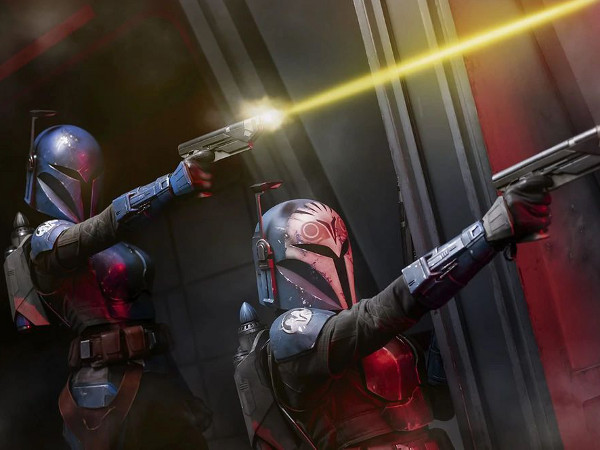
Im Bild links Koska Reeves und rechts Bo Katan. Auch wenn Bos Helm mit dem aufgemalten Eulengesicht spektakulärer erscheint, entschieden wir uns doch aus gutem Grund für Koskas Helm. Von Nikko Industries erwarben wir ein 3d File und da der Ausdruck über Dienstleister teurer als ein eigener Drucker gewesen wäre, erwarben wir in der Folge eine 3d-Drucker dazu. Leider ist so ein Helm recht groß, so dass wir ihn nicht in einem Stück drucken konnten.
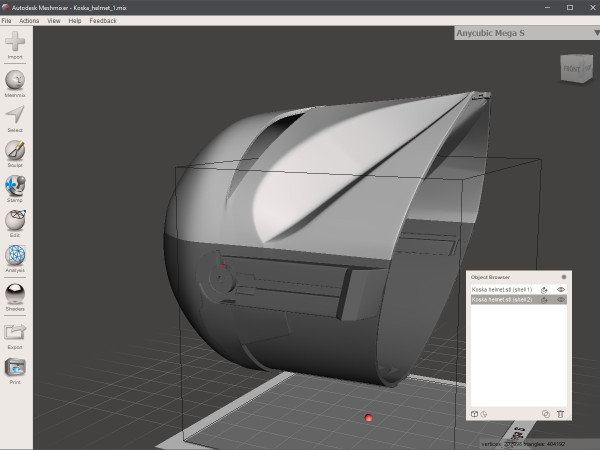
Mit der Freeware Meshmixer zerteilten wir den Helm in kleinere, druckbare Teile. Anleitungen hierzu findet man im Netz. Ein schönes Video findet man zB hier:
Die einzelnen Teile druckten wir dann mit PLA aus. Jeder Druck dauerte zwischen 7 und 11 Stunden. Wir mussten natürlich Lehrgeld bezahlen. Die Nivellierung des Druckbettes ist nicht so einfach und oftmals brauchte es viele Versuche, bis ein Druck überhaupt richtig begann, weil das PLA nicht an der Grundplatte haftete.
Außerdem brauchten einige Teile mit Überhängen eine Stützstrucktur. In Meshmixer kann man die automatisch berechnen lassen, die entstehenden Säulen sind jedoch nicht in jedem Fall wirklich brauchbar. So sieht die von Meshmixer berechnete Stützstrucktur des Stirnteils aus:
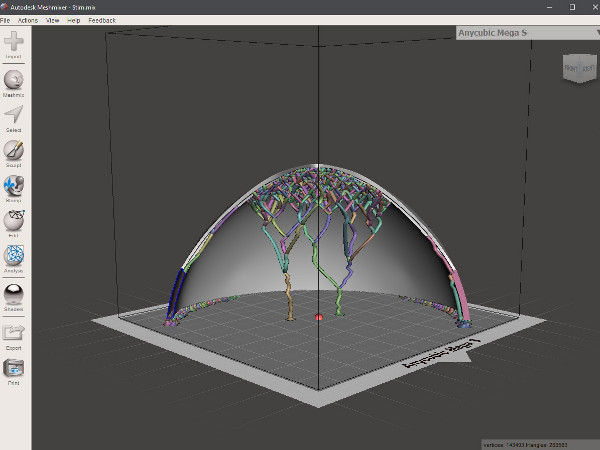
Und jetzt ein Bild des Druckes: Die Stützstrucktur ist völlig aufgefasert und hat drucktechnisch überhaupt gar nicht wie geplant funtioniert. Trotzdem konnte er die entscheidende Helmstruktur dann oben drauf drucken.
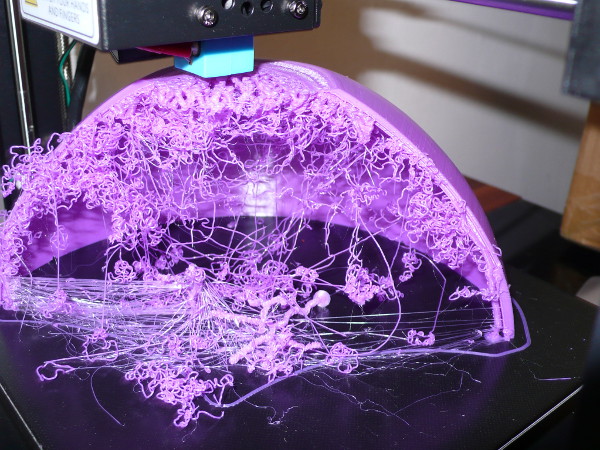
Ein Teil, der senkrecht gedruckt wurde, fiel nach 80 oder 90% um. Damit war der Druck logischerweise hin und sowohl viele Stunden als auch Material verschenkt.
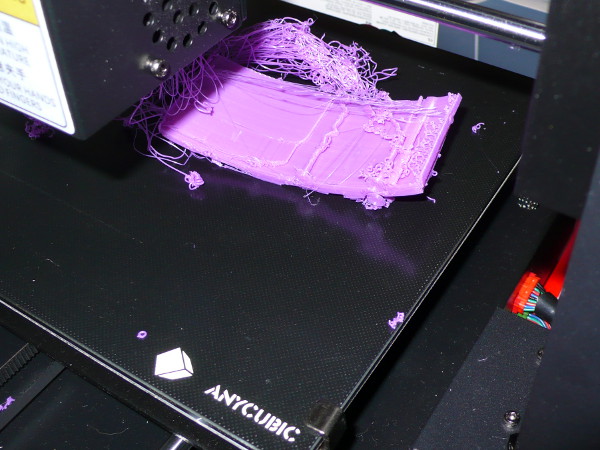
Wir fügten daraufhin großzügig manuell weitere Stützstruckturen hinzu und versuchten es erneut, diesmal erfolgreich, auch wenn nicht alle der Stützen gedruckt wurden.
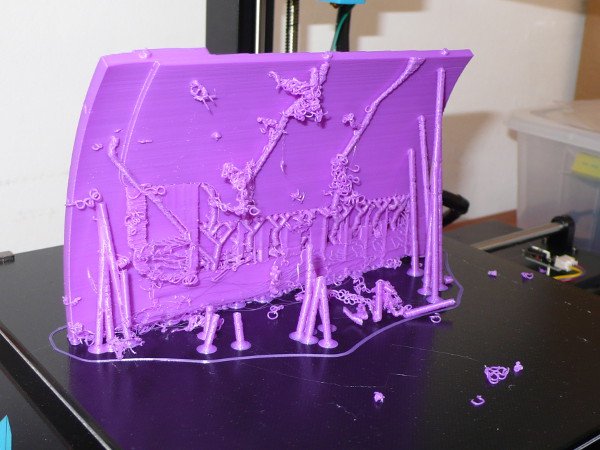
Die Ergebnisse waren im Großen und Ganzen akzeptabel. Dadurch, dass in Schichten gedruckt wird, sind diese hinterher leider auch im Druck zu sehen, das heißt hier hängt noch ein ordentlicher Rattenschwanz an Arbeit dran.
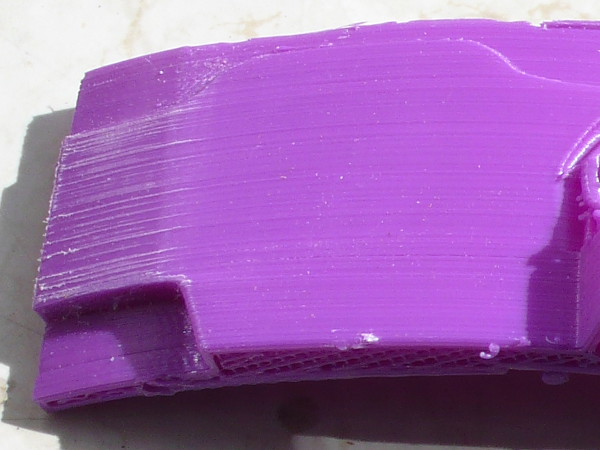
Die Stützstrucktur läßt sich mit normalem Werkzeug problemlos entfernen. Hier kamen ein Schraubenzieher und eine Zange zum Einsatz.
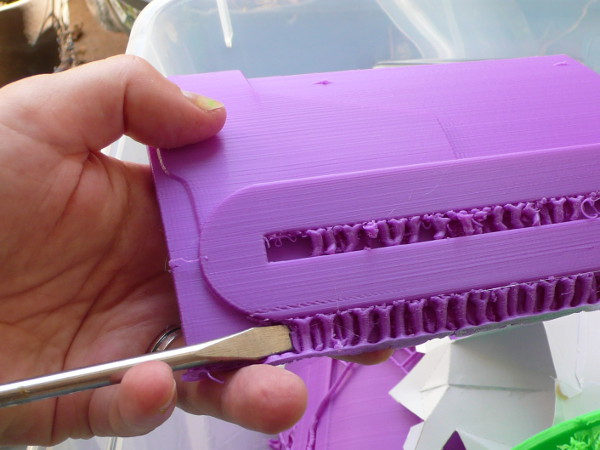
Die zurückbleibende Oberfläche sah allerdings extrem rau und unregelmäßig aus. Hier war also zunächst einmal Schleifarbeit zu leisten. Der Dremel für kleine Ecken hat das Problem, dass er mit hohen Drehzahlen arbeitet und dadurch Hitze entsteht. Diese wiederum kann das PLA zum Schmelzen bringen, was in aller Regel nicht erwünscht sein sollte. Allerdings kommt man ohne die vielen kleinen verschiedenen Spitzen des Dremels in den Ecken nicht wirklich gut zurecht. Behelfen kann man sich, indem man immer nur kurz auf einer Stelle schleift und alle paar Sekunden wechselt.
In der Fläche funktionieren der Exzenterschleifer sowie der Winkelschleifer ganz hervorragend, das PLA wird schön abgeschliffen ohne das Wärme entstünde. Es kam hier zu keinerlei Verformungen. Wir nutzten ein 120er Schleifpapier. Ansonsten wird empfohlen, manuell zu schleifen. Bei ABS funktioniert wohl auch Aceton zum Glätten ganz gut, das geht mit PLA jedoch nicht.
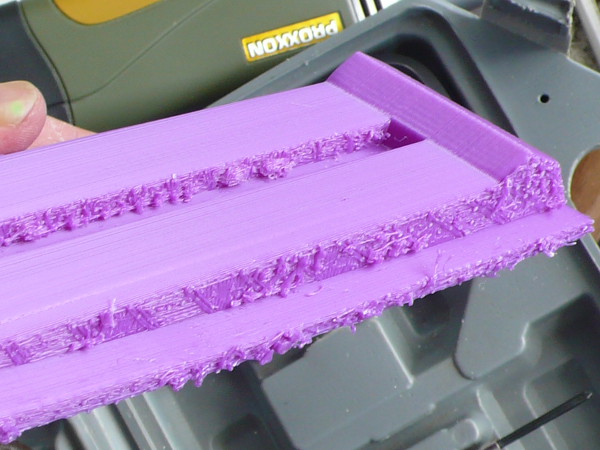
Nach einem Schleifdurchgang wurden die verbleibenden Rillen mit Presto 2K Polyesterspachtel zugespachtelt. Dieser wird nach Gewicht angerührt. Dabei verdunstet Styrol, man sollte eine Atemschutzmaske tragen. Das entstehende Gemisch hat eine relativ kurze Topfzeit von wenigen Minuten und muss dementsprechend schnell verarbeitet werden. Die Topfzeit hängt dabei mit der Menge des Härters zusammen: Mehr Härter heißt schnelleres Aushärten, nimmt man etwas weniger, so erkauft man sich etwas Verarbeitungszeit. Trotzdem empfiehlt es sich wohl, innerhalb der vorgegebenen Dosierungsbereiche zu bleiben. Für mich war es das 1. Mal und so muss man eben ein wenig probieren. Auf jeden Fall sollte man bei derartigen Projekten nur kleine Mengen auf einmal anrühren und dafür lieber mehrere Durchgänge machen. Zum Spachteln selbst eignen sich Japanspachtel sehr gut.
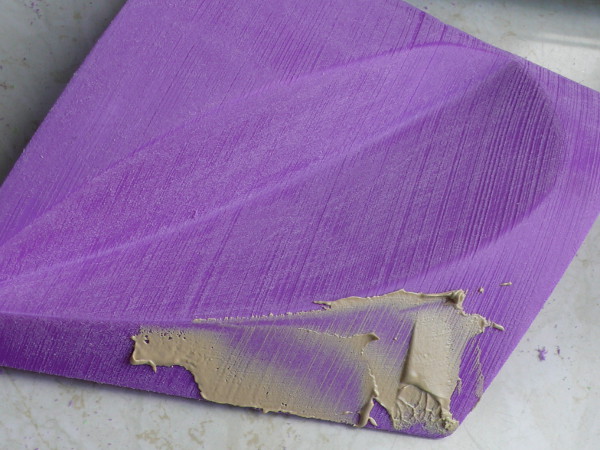
So sah das fertig gespachtelte Wangenteil vor dem Schleifen und nach dem Schleifen aus.
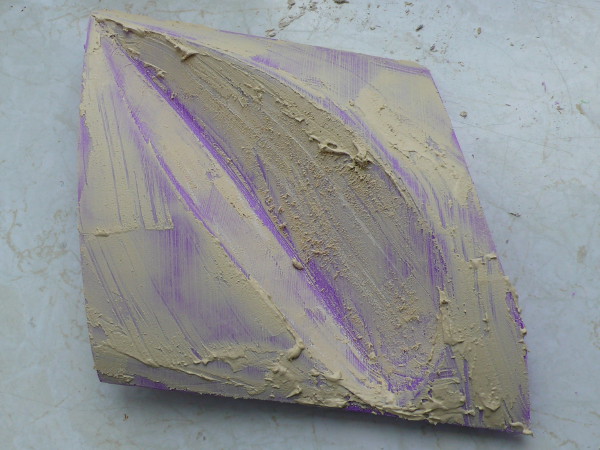
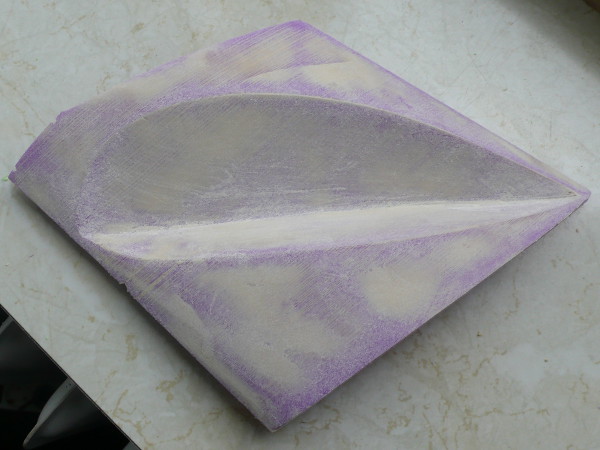
Wir druckten als nächstes den Rangefinder. Hierbei entschieden wir uns für die Option „Stützstrucktur generieren“, welche Cura anbietet. Im Ergebnis wird eine Wabenförmige Stützstrucktur unter den vertikalen Freihängen aufgebaut.

Diese lässt sich sehr leicht entfernen, da die Verbindung zum Druck nur über dünne Brücken erfolgt. Das Ergebnis ist dann eine deutlich sauberere Fläche, als dies bei der vorherigen Lösung der Fall war.
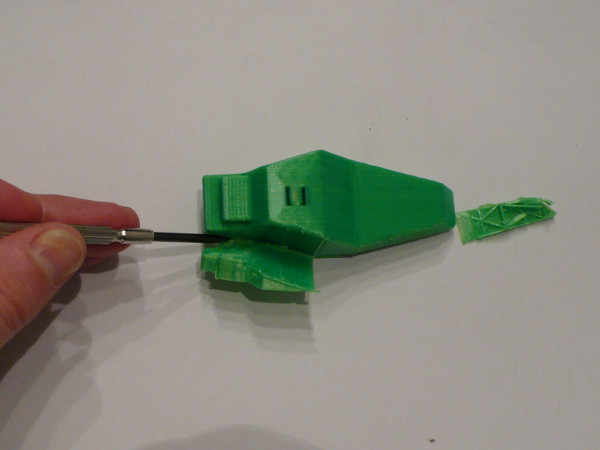
Beim Ausdruck des Visors hatten wir trotz unendlichen Nivellierens des Druckbettes und ansonsten unveränderten Parametern plötzlich arge Probleme mit der Druckbetthaftung. Lösen ließ sich die Problematik schlussendlich nur durch einen Strauß bunter Maßnahmen: Wir verringerten die Druckgeschwindigkeit der ersten Schichten und stellten hierzu den Lüfter aus. Der Druckplattenhaftungstyp wurde auf „Brim“ geändert. Hierbei wird eine großflächiges Bett unter dem eigentlichen Druck gedruckt. Wir experimentierten noch mit der Ausrichtung des Teiles und stellten fest, dass man durch eine steilere Position nur die halbe Druckzeit brauchte, da deutlich weniger Stützstrucktur notwendig ist. So sammelt man durch Trial-and-Error so seine Erfahrungen.
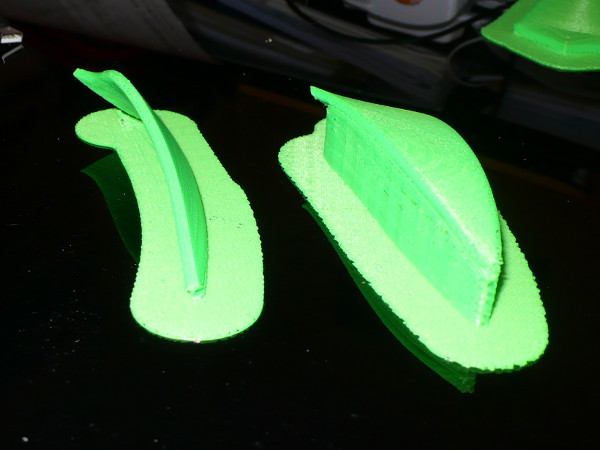
Im nächsten Schritt wurden die insgesamt 7 Teile des Helmes verklebt. Beim Auseinanderschneiden des Helmes fügten wir jeweils an den Schnittkanten kleine Stifte und auf der Gegenseite entsprechende Löcher ein. Dies funktionierte ausreichend gut, ist aber sicher nicht der Königsweg. Die Schnitte selbst waren der Einfachheit halber alle glatt. Es wäre sicherlich sinnvoller, hier komplexere Verzahnungen in allen Ebenen einzufügen, da uns die Programme jedoch völlig neu waren, wollten wir es so einfach wie nur möglich halten.
Zum Kleben benutzten wir nach etwas Recherche
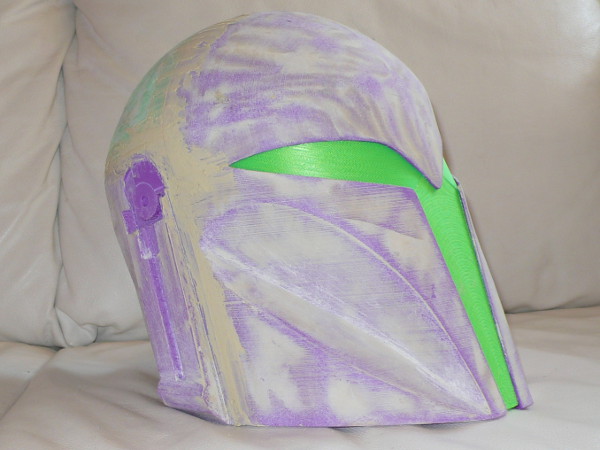
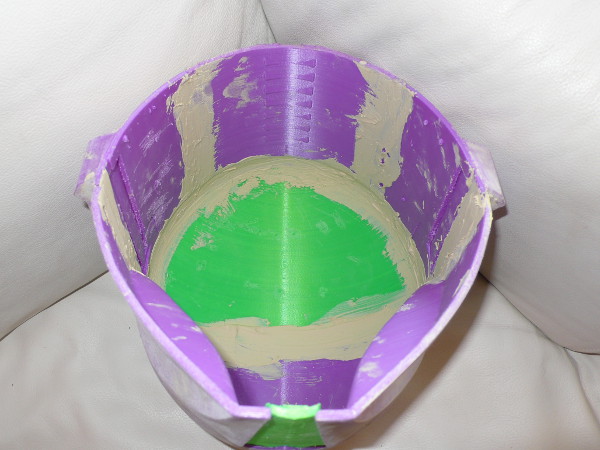
Es folgte eine lange Phase von Spachteln/Schleifen, Spachteln/Schleifen, Spachteln.. Wir verwendeten Presto 2K Polyesterspachtel. Für die Verarbeitung raten wir dringend zur Verwendung eines adäquaten Atemschutzes! Wir verwenden von 3M die 6200 mit A2 Filter beim Anmischen des Spachtels. Der A2 filtert organische Dämpfe weg. Zum Schleifen genügt dann auch eine ganz normale FFP2 Maske, die ist heutzutage einzeln deutlich günstiger zu bekommen als die Einlagen für die 6200. Aber wie gesagt: Achtet auf den Eigenschutz! Wir haben ansonsten diese Arbeiten immer nur im Freien durchgeführt. Die Dämpfe bzw Stäube bekommt man tagelang nicht aus der Wohnung.
Irgendwie fand sich immer noch eine Stelle, an der man dachte, da müsste man noch mal was machen. Aber gut, irgendwann muss man das Ganze als fertig definieren. Und so sah der Helm dann aus:
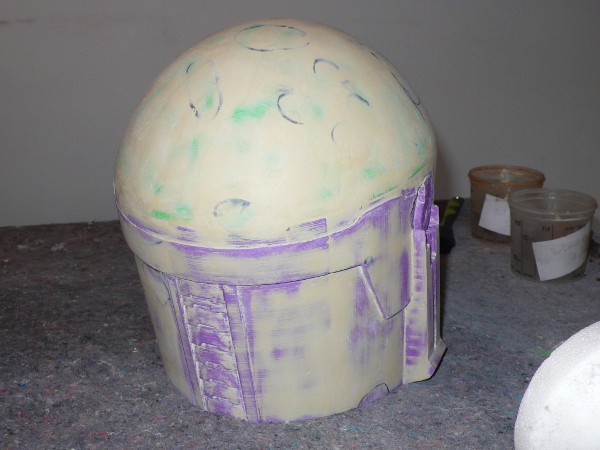
Damit die SIlikonform sich später gut wieder lösen ließe, wurde der Helm nun mit Mann Ease Release 300 dünn eingesprüht.
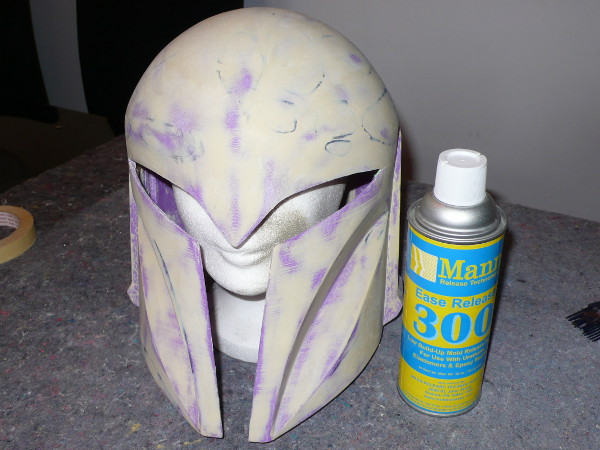
Nun musste der Helm abgeformt werden. Hierzu kam für die Mold wiederum Rebound 25 von Smooth On zum Einsatz. Für die 1. Schicht mischte ich je XXX ml Part A und Part B. THINNER??? Nach sorgfältigem Verrühren wurde es mit einem Pinsel relativ dünn auf den Helm aufgetragen. Schicht 2 erfolgte analog. Man sollte so lange warrten, bis die untere Schicht "sticky" ist, d.h. wenn man mit dem (behandschuhten) Finger darauf tippt, sollte es noch leicht klebrig sein. Dann verbinden sich die Schichten gut.
Schicht 1
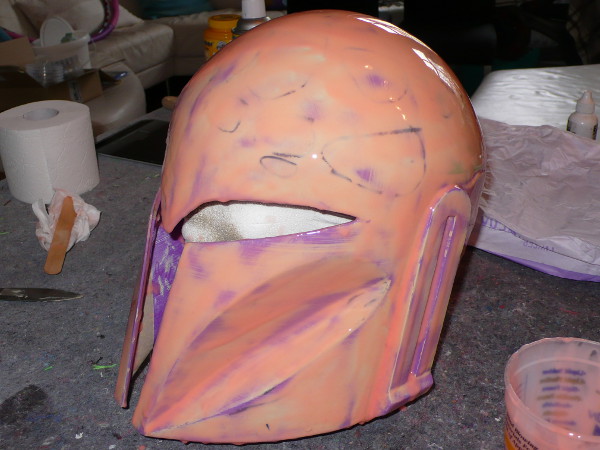
Schicht 2
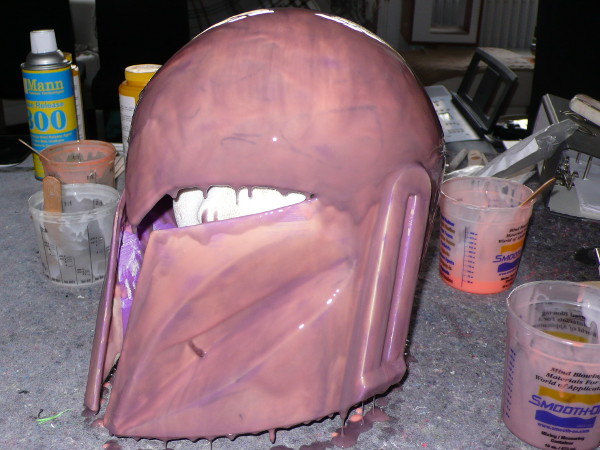
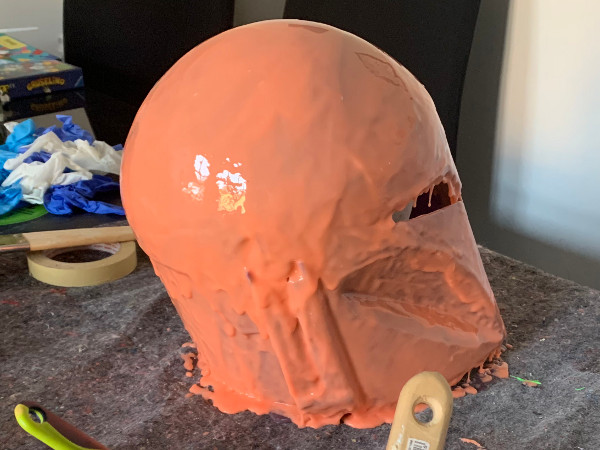
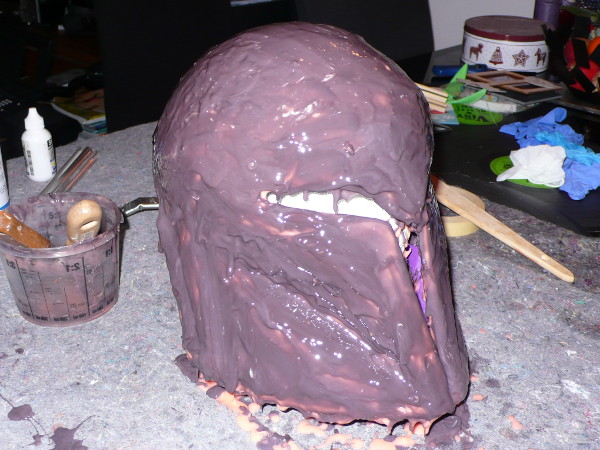
Nach Aushärtung über Nacht musste nun die feste Mother Mold als Stütze für das weiche und biegsame Silikon gefertigt werden. Wir konzipierten sie in 3 Teilen: Eine Art Deckel oben und dazu 2 Seitenteile. Für die Mother Mold verwendete ich Plasti-Paste. Dieses kann man entweder nach Volumen (1A : 3B) mischen, oder aber nach Gewicht im Verhältnis ( X : X ). Mir schien Gewicht in disem Fall praktikabler zu sein. Beide Komponenten wurden also mit der Küchenwaage abgewogen, mit einem Holzrührstab zusammengemischt
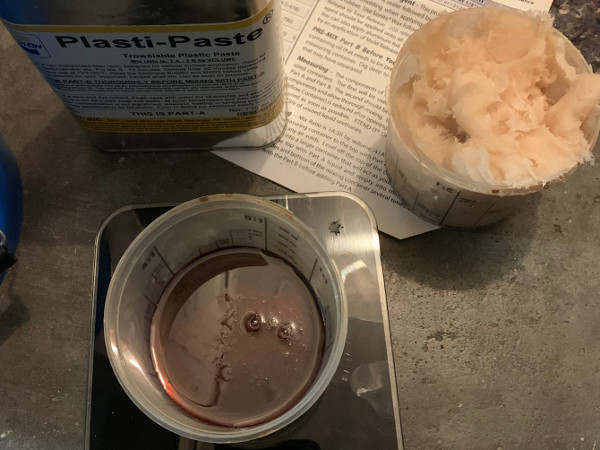
und danach dick aufgetragen. Nach circa 90 Minuten ist es bretthart und stabilisiert die Silikonform. Um die Verbindung zwichen den 3 Teilen zu gewährleisten, arbeitete ich Schrauben und Muttern ein.
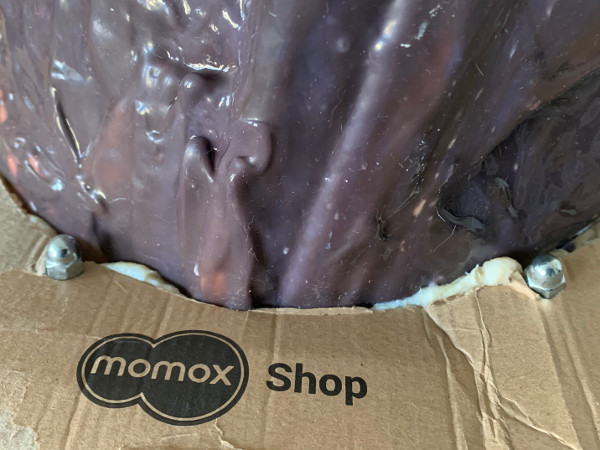
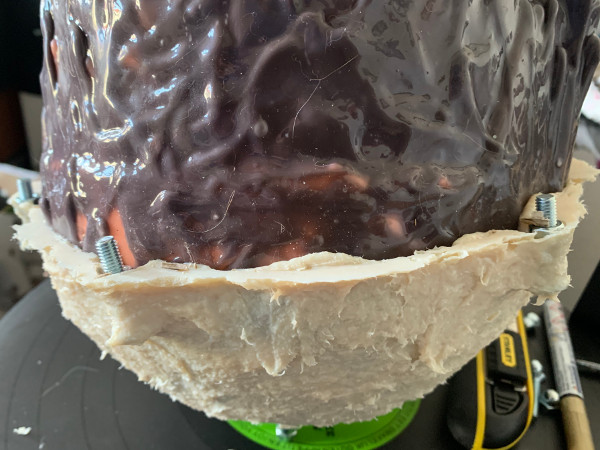
Nach Vorbehandlung mit Release-Agent wurde der Helm mit Smooth-Cast 65D gegossen. Es wird zu gleichen Teilen nach Volumen gemischt, muss für ca. 20 Sekunden gründlich verrührt werden und wird dann in die Silikonform gegossen und dort geschwenkt und verteilt. Pot-Life sind 2,5 Minuten, d.h. danach ist das Plastik so viskös, dass es nicht weiter umverteilt werden kann. Vollständig durchgehärtet ist das Ganze nach 15 Minuten. Je nach gewünschter Stärke sollten insgesamt 3-4 Schichten gegossen werden. Dabei ist es von Vorteil, wenn die vorherige Schicht noch leicht „klebrig“ ist, damit die Schichten sich optimal verbinden.
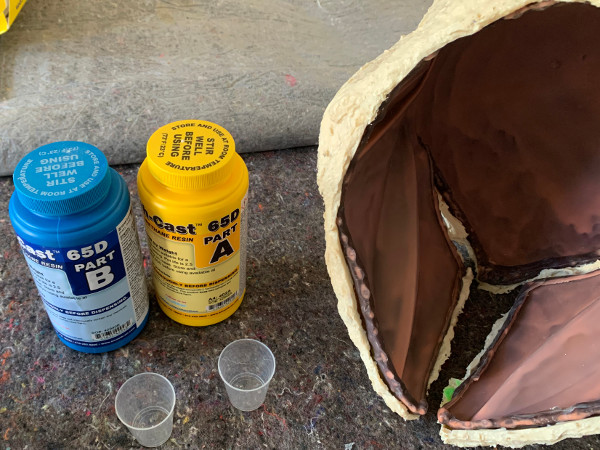
Es folgte das Demolding. Ein spannender Moment..
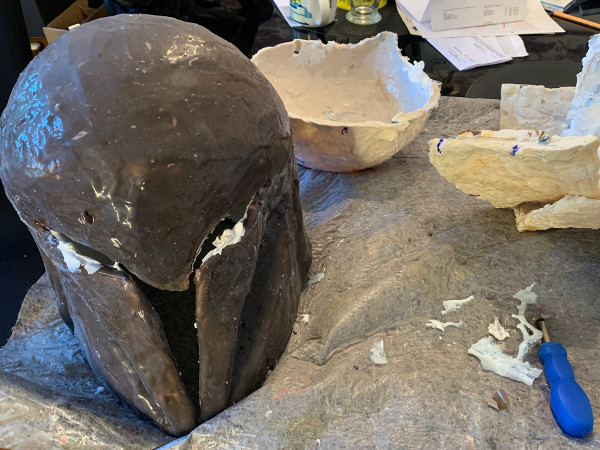
Tja, was soll ich sagen?? Das Ergebnis war super enttäuschend! Wir hatten hin und her überlegt und mein Konzept war, den Visor nicht einzubauen. Irgendwie hatte ich die Hoffnung, die Kanten so besonders gut abbilden zu können. Dieses hat sich wie man sieht leider überhaupt nicht funktioniert. Zwischen den Augen fehlt die Spitze völlig.
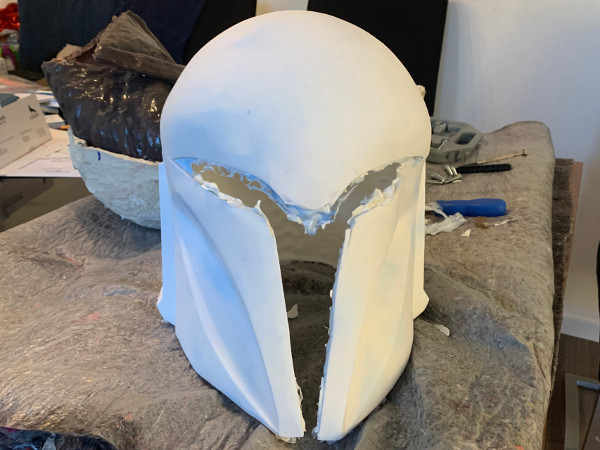
*****