Wandverkleidung aus Lichtbeton
Durch Zufall stießen wir im Netz auf eine spannende Sache: Lichtbeton! Es gibt da in den Tiefen des Netzes eine Firma, die ein Betonprodukt mit eingelassenen Lichtleitfasern entwickelt hat. Die Betonplatten haben eine Stärke von 20 bzw 30 mm. Eingelassen sind 200.000 optische Fasern /m² mit einem Durchmesser von 0,5 mm. Im Ergebnis sieht das Ganze dann so aus:
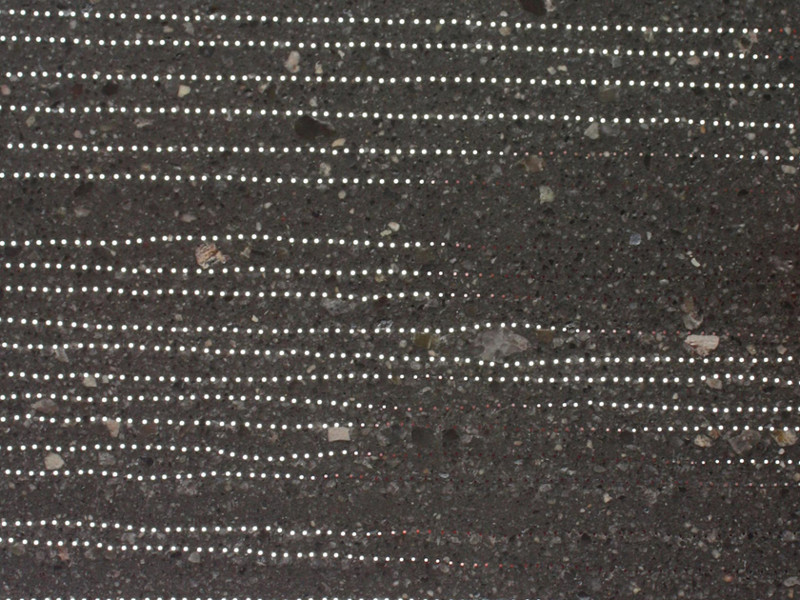
Da der Neubau unseres HQ anstand, war dieser Lichtbeton für uns natürlich sofort interessant und wir haben eine Anfrage gestartet um zu eruieren, ob eine Möglichkeit bestünde, hier professionell Akzente setzen zu lassen. Leider haben wir als sehr kleine Kunden keine richtige Beachtung gefunden und konnten hier nicht weiter kommen. Oder anders gesagt, wir haben dann nicht weiter nach gebohrt, da uns selbst der Stolz gepackt hat. Vermutlich wären die Preise eh viel zu hoch gewesen, besagte Firma stattet immerhin internationale Hochglanz-Projekte aus. Und auch wenn unser HQ nicht in Abu-Dhabi steht und unsere Expertise sich auf die Youtube-Akademie beschränkt, so schien es uns doch kein Ding der Unmöglichkeit zu sein. So ein bisschen tüfteln und ein DIY-Projekt sind doch auch was Feines und auch ein Scheitern kann ja was Süßes haben sofern man alles in den Kampf hineingeworfen hat. Es wertet im Endeffekt das HQ doch ungemein auf, wenn man die entscheidenden Dinge selbst gemacht hat.
Wir begannen also zu experimentieren. Wir bestellten uns Lichtfasern, schnitten die in handliche Stücke, durchlöcherten damit den Boden eines Plastikbechers und gossen diesen zunächst einmal der Einfachheit halber mit SmoothOn aus. Und siehe da: Die Fasern leiteten. Wir wiederholten das Ganze mit einem Fließzement von Boesner und hatten unser erstes kleines Stück Lichtbeton. Ein Haken hinter Schritt 1. Leider haben wir hiervon kein Foto.
Schritt 2, der eigentlich größte Schritt, bestand nun in der gedanklichen Konstruktion der herzustellenden Platten. In der großen Industrie funktioniert das Ganze so, dass Lichtfasern in einer großen Form quer gespannt werden. Von oben wird dann Beton eingefüllt und es entsteht ein einziger großer Block mit Lichtfasern. Dieser wird danach mit einer Monster Kreissäge in Platten gesägt.
Da ein derartiges Verfahren für uns eher nicht in Frage kam – Sohnemann und Monsterkreissäge sind keine kompatible Kombination sofern man das Kind noch behalten möchte – brauchten wir andere Lösungen.
Die Frage war, wie befestigt man die Lichtfasern für den Prozess des Betongießens? Wenn man aus der Industrievariante die Säge herausnimmt könnte man eine einzelne Platte gießen. Die Probleme sind in dieser Anordnung einmal die Befestigung der Lichtfasern. Bei einer derartigen Vielzahl von Fasern kann man nicht jede einzelne Faser irgendwo einspannen oder ähnliches, es muss eine schnelle Lösung geben. Des Weiteren ist es relativ unpraktisch, in der senkrechten Anordnung eine einzelne Platte zu gießen. Die Seiten wo die Lichtfasern verankert wären müssten ja gleichzeitig die Schalungsform sein. Klingt schwierig. Möglicherweise gibt es hierzu auch eine schlaue und praktikable Lösung, allein wir haben sie nicht entdeckt.
Wir beschlossen also, den Prozess um 90° zu drehen und die Platte flach zu gießen. Da wir keinen Block gießen würden, sondern nur eine einzelne Platte von 1-2 cm Stärke, könnten die Lichtfasern alleine durch ihre eigene Steifigkeit stehen und müssten keine 2. Verankerung an der Gegenseite bekommen. Schon mal 1 Problem weniger.
Wie verankert man nun die Fasern schnell und effizient an der Unterseite der Schalungsform? Am schnellsten würde es gehen, wenn man die 3-5 cm langen Stücke einfach in irgendetwas hinein stecken könnte, das weich genug wäre um sie problemlos aufzunehmen, aber stabil genug um sie dann zu halten. Und sich danach außerdem problemlos wieder vom Beton lösen lassen würde. Zum Beispiel Sand könnte die ersten beiden Anforderungen problemlos erfüllen. Bei der Ausschalung wäre er wohl eher nachteilig, aber letzten Endes könnte diese Seite der Platte ja die Rückseite sein und somit wäre die Optik absolut zweitrangig.
Wir entschieden uns aber für eine andere Variante: Wir suchten eine geleeartige Substanz, welche die oben genannten Voraussetzungen erfüllen könnte. Einen Versuch führten wir mit Tortenguss durch. Der Boden eines Gefäßes wurde ca. 1 cm hoch mit Tortenguss aufgefüllt. Nach Abkühlen und Aushärten steckten wir Lichtfasern hinein und füllten dann eine ca. 1 cm starke Schicht Fließbeton ein. Die Handhabung gelang völlig problemlos, der Beton härtete gut aus und ließ sich perfekt ausschalen und vom Tortenguss befreien. Das Ergebnis war so wie erhofft.
Der Ansatz stand zunächst einmal, wir experimentierten noch mit Stärke und machten den nächsten Versuch dann mit Kartoffelstärke. Sie hat den Vorteil, relativ günstig zu sein. Nach einem 1. Versuch, der geneigten Köchen vermutlich vor Lachen Tränen in die Augen getrieben hätte stellten wir fest, dass man die Stärke in etwas kaltes Wasser einrühren muss und erst danach dann in warmes. Man lernt halt ständig irgendetwas hinzu..
Außerdem probierten wir einen anderen Beton aus und zwar SysCompound SVi, einen Hochleistungsbeton von Consulta. Dabei handelt es sich um Zement als Bindemittel mit Zugabe von Braunkohle-Flugasche. Durch die extrem feine Flugasche ist der Mörtel auch ohne die Zugabe von Hochleistungsfließmittel extrem fließfähig. Der Hersteller empfiehlt zum Mischen die Verwendung eines Zwangsmischers oder eines Handmischers mit zwei entgegengesetzt laufenden Rührstäben. Dies ist insofern wichtig, als es sich laut Angabe durch Intensivmischung verflüssigt bzw. dass es nach dem Mischen bei nochmals verringertem Wasseranspruch aus der „Kittphase“ sofort in die „Verschmelzungsphase“ (zähfließend-verkittend) übergeht. Dies aber nur bei geeigneter Betonverdichtungstechnologie, welche uns initial nicht zur Verfügung stand. Einen Zwangsmischer hat man logischerweise nicht zufällig mal im Keller stehen. Wir probierten es zuerst einmal mit "Handrührung" und stellten fest, dass dies in der Tat nicht wirklich funktioniert. Die "Verflüssigung" konnten wir nicht erreichen und mussten deutlich mehr Wasser als angegeben zugeben als angegeben.
Aber fangen wir mal vorne an: Wir bauten eine Schalungsform in 20 x 20 cm aus beschichteter Spanplatte. Die Stöße wurden mit einer Silikonfuge abgedichtet. Wir füllten die Form ca. 1,5 cm hoch mit angerührter Kartoffelstärke und ließen das Ganze über Nacht fest werden.
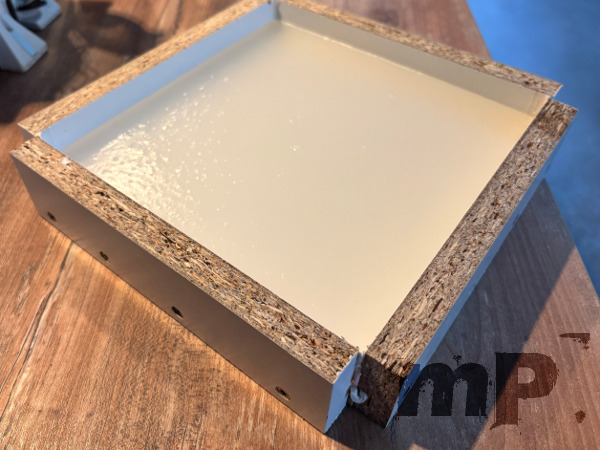
So war genug Zeit, um die Lichtfasern in ca. 3 cm lange Stücke zu schneiden, als Hilfsmittel diente sich der metallene Einsatz der Knoblauchpresse an. Wir hatten Lichtfasern in den Stärken 0,5 mm, 0,75 mm und 1,0 mm.
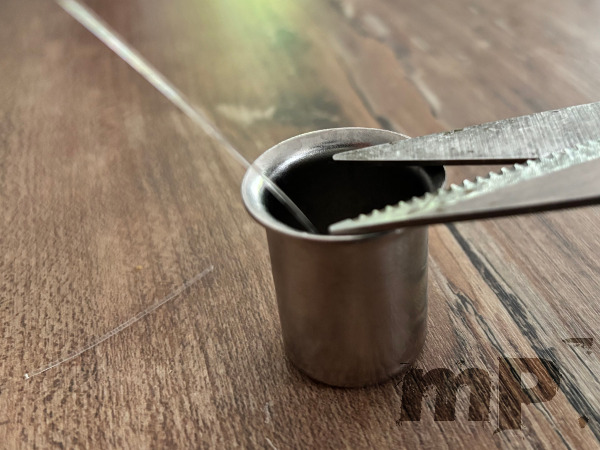
Im nächsten Schritt wurde das SysCompound SVi händisch angerührt, hierfür wurde - wie gesagt - eigentlich zu viel Wasser genommen, um doch noch eine fließfähige Konsistenz zu erreichen. Das Gießen in die From klappte dann problemlos. Die Frage war ja, ob das Gelbett halten würde, oder ob der Beton sich in dieses hineinwühlen würde, womit dann direkt alles gescheitert wäre. Aber es klappte sehr gut, das Bett hielt und der Beton verteilte sich gleichmäßig.
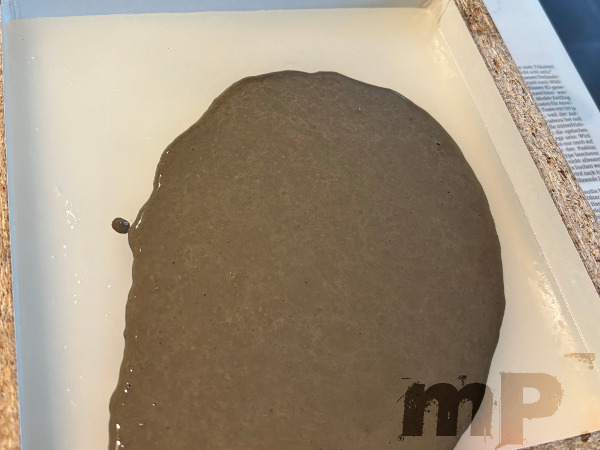
Nach einer dünneren 1. Schicht legten wir zur Stabilisierung der Platte ein Armierungsgewebe ein. Dies wäre selbstverständlich für die Größe von 20 x 20 cm nicht nötig gewesen, aber letzten Endes ging es ja um eine Machbarkeitsstudie für größere Platten. Jetzt kam der Zeitraubende Teil: Die Lichtfasern mussten einzeln per Hand eingebracht werden. Das gelang prinzipell problemlos. Das Gelbett bildete an der Oberfläche eine Art "Haut", wie ein klassischer Vanillepudding. Dieses ließ sich mit der starren Lichtfaser durchstechen und nach dem gut fühlbaren Widerstandsverlust wusste man, dass man tief genug ist und die Faser am Ende durch die Platte durch gehen würde. Die Fasern von 0,5 mm waren hierfür grenzwertig dünn, sie bogen sich leicht, weshalb es bei ihnen insofern etwas anstrengender war. Nachdem alle knapp 200 Fasern an Ort und Stelle waren - wofür schon die eine oder andere Minute ins Land gezogen war - wurde die Form bis zum Rand mit Beton aufgefüllt. Dabei hielten die Fasern gut, der Beton verteilte sich und keine Faser kippte um.
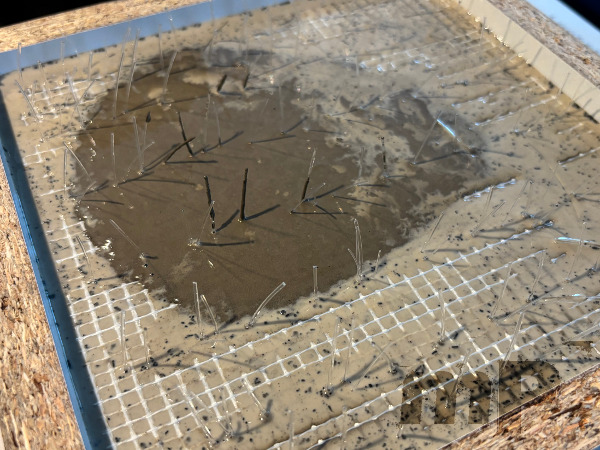
Natürlich stellt sich die Frage, was man hinterher mit dem fertigen Lichtbeton anstellt. Im Netz finden sich viele schöne Fotos, bei denen Lichtbeton als stylische Wandverkleidung mit farbiger Hinterleuchtung genutzt wird. Wie bekommt man die Platte also hängend befestigt? Möglichkeiten gibt es sicher viele, wir entschieden uns für diesen Test für eine Schrankaufhängung. Die Schrankaufhänger haben Löcher, in die M4 Schrauben passen. Hierfür sollten Gewindemuffen in die Platte eingegossen werden.
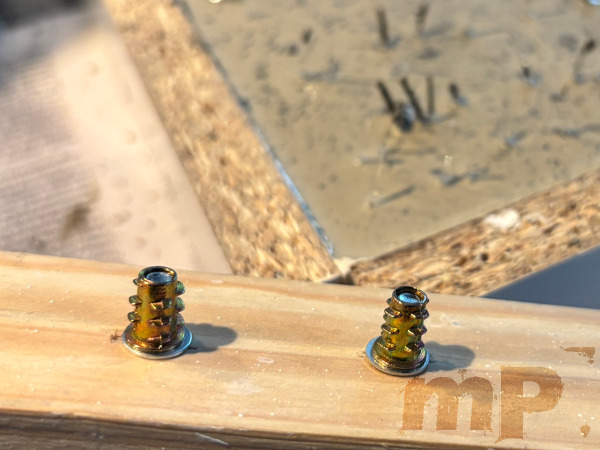
Die Gewindemuffen wurden per Schraube an einer Holzlatte befestigt, sodann wurde die Latte umgekehrt auf der Schalungsform festgeschraubt, so dass die Gewindemuffen sich vollständig im Beton befunden haben. Dabei hat sie die Lichtfasern in diesem Bereich natürlich nach unten in den Beton hineingedrückt, die Lösung ist also insofern noch suboptimal. Allerdings lässt sich das Problem mit relativ begrenztem Aufwand lösen.
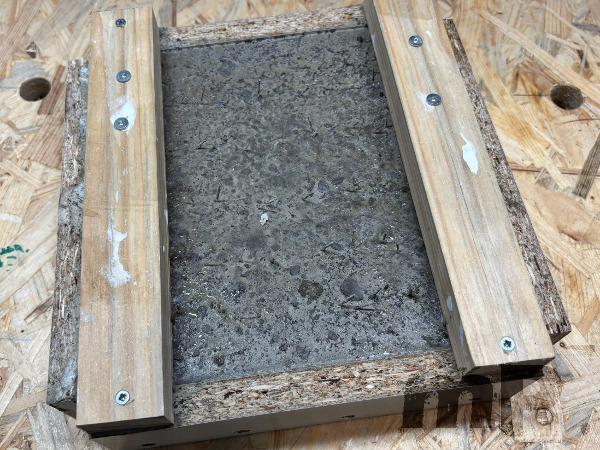
Nach 3 Tagen ging es ans Ausschalen. Das Gebilde so lange mehr oder weniger unbeachtet in der Ecke stehen zu lassen ist schon eine Herausforderung.. Zuerst wurden die Latten wieder gelöst. Sie gingen leicht ab. Die Gewindemuffen saßen wunderbar im Beton.
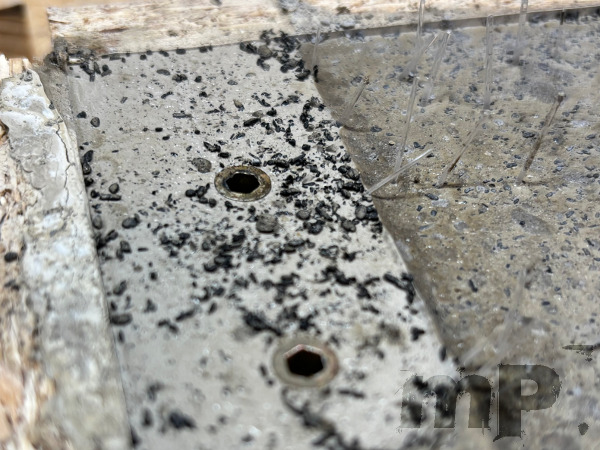
Nach Ablösen einer seitlichen Leiste sieht man das Konstrukt im Querschnitt. Ein interessantes Bild.
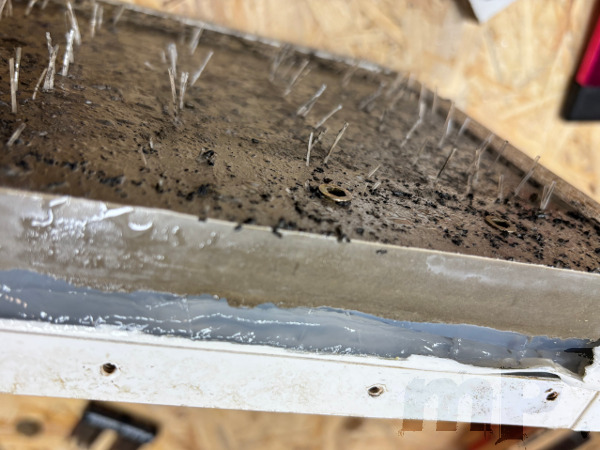
Wenn man alles umdreht, hat man das Geleebett vor sich. Es lässt sich mit etwas Wasser und den Händen oder auch einer Bürste problemlos entfernen. Auf dem Foto ist schon ein dicker Wasserstrahl durchgepflügt.
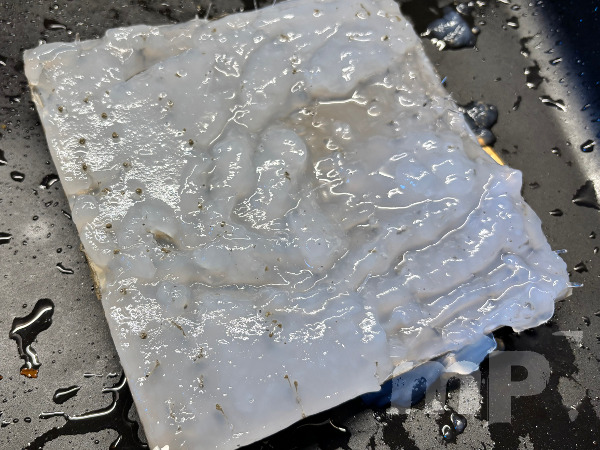
Nach Säuberung sah die Platte dann wie folgt aus:
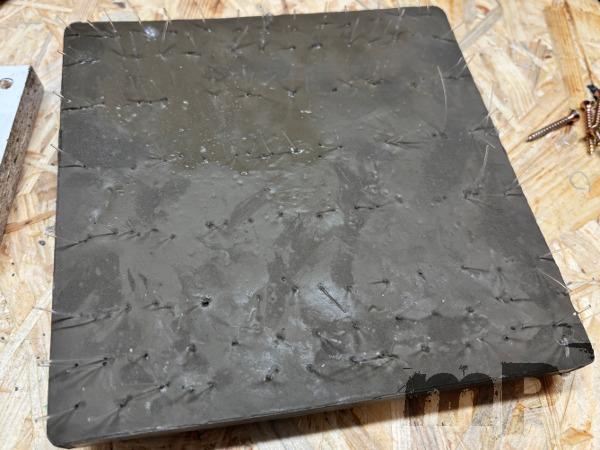
Die überstehenden Lichtfasern wurden mit der Flex vorsichtig gekürzt. Danach wurde mit dem Exzenterschleifer in mehreren Schleifgängen bis 240er Körnung runter geschliffen. Auf der Rückseite konnten dann die Schrankaufhänger montiert werden. Die Gegenstücke wurden der Einfachheit halber auf einer Holzlatte montiert.
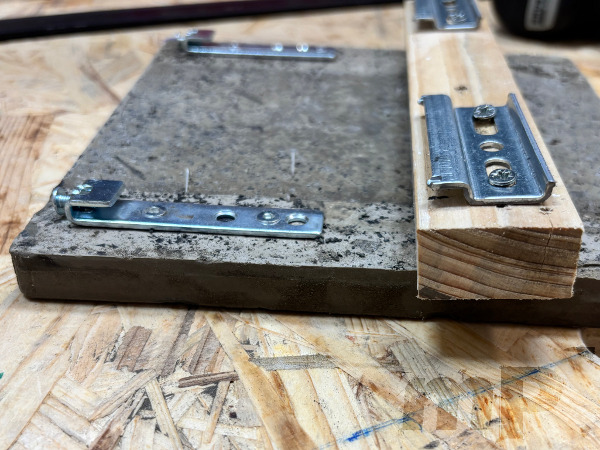
Ein erster Blick ins Gegenlicht.
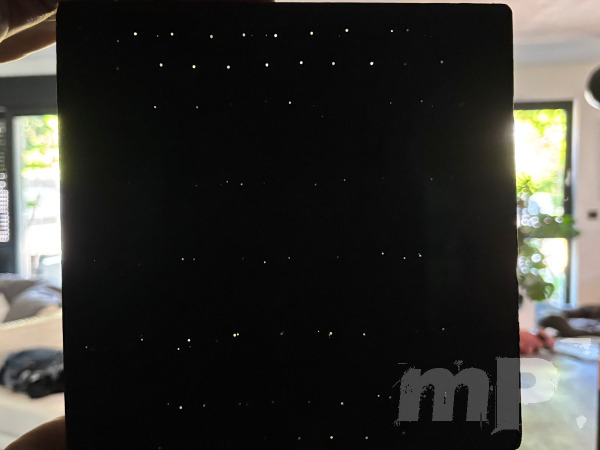
Man sieht, dass an den Seiten, wo die Latten für die Gewindemuffen gesessen haben, die Lichtleitung doch arg in Mitleidenschaft gezogen wurde. Die Verteilung der Fasern ist ehrlich gesagt nicht mit großer Akribie erfolgt, auch das sieht man. Und letzten Endes muss man diskutieren über die Zahl der Fasern, die man eingießen möchte. 200.000 Fasern pro Quadratmeter wie in einem professionellen Setting sind sicherlich keine Überlegung wert. Hier sind es ca. 1000 pro Quadratmeter. Bei diesem Versuch hat es keine große Rolle gespielt, aber in größerem Maßstab gedacht sind deutlich mehr Fasern irgendwann auch teurer und nebenbei bemerkt eine wirkliche Geduldsprobe!
*****